Necessary Pipe Welding Assessment Tips for Quality Control
In the realm of pipeline building and construction, the honesty of welds holds extremely important importance to make certain the safety and security and effectiveness of the entire system. From gas to refined oil items, pipelines form the lifeline of various sectors. Just how can one ensure the high quality of these welds that attach the pipe areas? The response hinges on thorough examination methods and adherence to strict quality control standards. By understanding the essential pipe welding inspection pointers, specialists can avoid prospective hazards, decrease costly fixings, and promote the reliability of these critical frameworks.
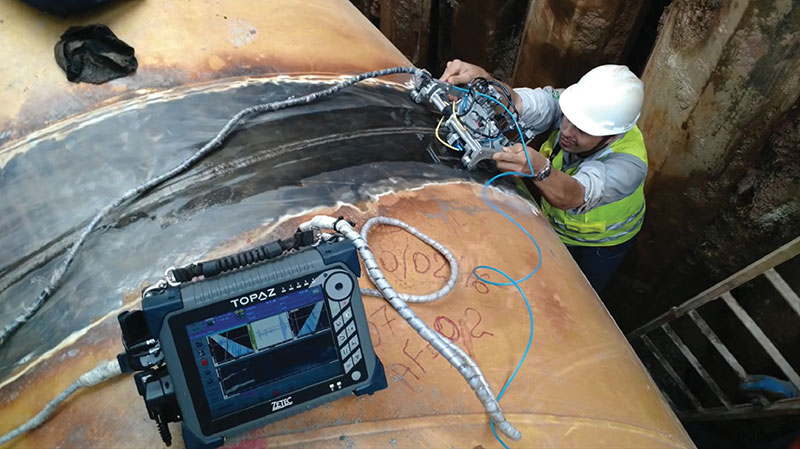
Relevance of Welding Examination
Welding evaluation plays a vital duty in making sure the architectural stability and safety and security of pipe systems. By thoroughly examining welds, assessors can determine any type of issues or imperfections that might jeopardize the integrity of the pipeline. These examinations are necessary for preventing leakages, ruptures, and other possibly catastrophic failures that can result in environmental damage, economic losses, and also loss of life.
The value of welding examination can not be overstated, as the high quality of welds straight influences the overall performance and durability of the pipe. Through non-destructive testing techniques such as aesthetic examination, ultrasonic screening, radiography, and magnetic particle testing, examiners can find flaws that may not be visible to the naked eye. By recognizing and addressing these issues at an early stage, welding assessment assists to make certain that pipes meet industry standards and regulatory requirements.
Inevitably, welding inspection is a vital element of top quality guarantee in pipe building, upkeep, and repair service (Pipeline Welding Inspection). By supporting rigorous examination criteria, sector experts can reduce risks and promote the safety and security and dependability of pipeline systems
Usual Welding Flaws
Among the obstacles faced in pipeline welding, usual issues can considerably affect the architectural honesty and performance of the welded joints. Splits in the weld can propagate over time, jeopardizing the architectural honesty of the pipe. Spotting and dealing with these typical issues through detailed inspection and high quality control procedures are necessary for making sure the dependability and safety and security of pipe welds.
Inspection Techniques for Pipelines


In guaranteeing the structural stability and dependability of pipe welds, the application of extensive assessment strategies is extremely important. Numerous examination approaches are used to detect potential defects and ensure the overall top quality of the welds. Non-destructive screening (NDT) strategies such as radiographic screening, ultrasonic testing, magnetic bit testing, and liquid penetrant screening are generally used in pipe welding examination. Radiographic screening includes making use of X-rays or gamma rays to discover interior defects, while ultrasonic screening makes use of high-frequency audio waves to determine imperfections. Magnetic particle screening is reliable for spotting surface-breaking defects, and fluid penetrant screening is used to detect surface area fractures. Visual inspection is additionally necessary in pipeline welding to identify any kind of noticeable defects or suspensions. In addition, automated evaluation techniques using sophisticated innovations like robotics and drones are progressively being used to enhance the performance and accuracy of pipeline evaluations. By utilizing a mix of these examination techniques, pipeline weld quality can be ensured, Go Here and prospective concerns can be reduced prior to they rise right into bigger issues.
Ensuring Quality Control Standards
To promote rigid quality control criteria in pipe building, meticulous adherence to developed industry methods and guidelines is crucial. Quality assurance in welding processes requires a detailed approach including various stages of pipe construction. Making certain the quality of welds entails using certified welders, appropriate welding procedures, and adherence to industry criteria such as those set check here by the American Oil Institute (API) and the American Culture of Mechanical Engineers (ASME) Examination and testing play a crucial duty in verifying the stability of welds, with strategies like non-destructive testing (NDT) being vital for spotting potential defects. Furthermore, keeping detailed paperwork throughout the welding procedure is essential for traceability and quality control functions. Applying a durable quality administration system that consists of normal audits and reviews can even more improve the total quality control requirements in pipeline welding. By focusing on adherence to these requirements, stakeholders can make certain the integrity and safety of pipeline systems for the long term.
Preventing Pricey Repair Services
Provided the essential importance of maintaining strict high quality guarantee criteria in pipe construction, a proactive method to avoiding expensive repair work is necessary. Routine upkeep checks and tracking of ecological aspects that might affect the stability of the pipeline are likewise vital in protecting against pricey repair services. By spending in preventative procedures and prioritizing high quality assurance at every stage of the pipe welding procedure, business can reduce the risk of expensive repairs and ensure the long-lasting reliability of their infrastructure.
Conclusion
Finally, adherence to correct welding examination strategies is necessary for making sure the quality and honesty of pipes. By determining common welding issues and carrying out detailed evaluation processes, expensive fixings can be avoided, and quality assurance criteria can be met - Pipeline Welding Inspection. It is the original source important for pipe welders to focus on inspection treatments to preserve the safety and integrity of the facilities they are servicing
The significance of welding examination can not be overemphasized, as the high quality of welds directly affects the overall efficiency and longevity of the pipeline. Non-destructive screening (NDT) methods such as radiographic screening, ultrasonic testing, magnetic bit testing, and fluid penetrant screening are typically made use of in pipeline welding examination. Visual assessment is also necessary in pipeline welding to determine any kind of visible problems or suspensions. Furthermore, automated evaluation techniques making use of advanced innovations like drones and robotics are increasingly being utilized to boost the efficiency and accuracy of pipeline examinations.In conclusion, adherence to appropriate welding examination strategies is essential for making sure the top quality and honesty of pipelines.